In our recent blog, Choosing a Linear Accelerator: The Evolving Landscape in 2025, we explored…
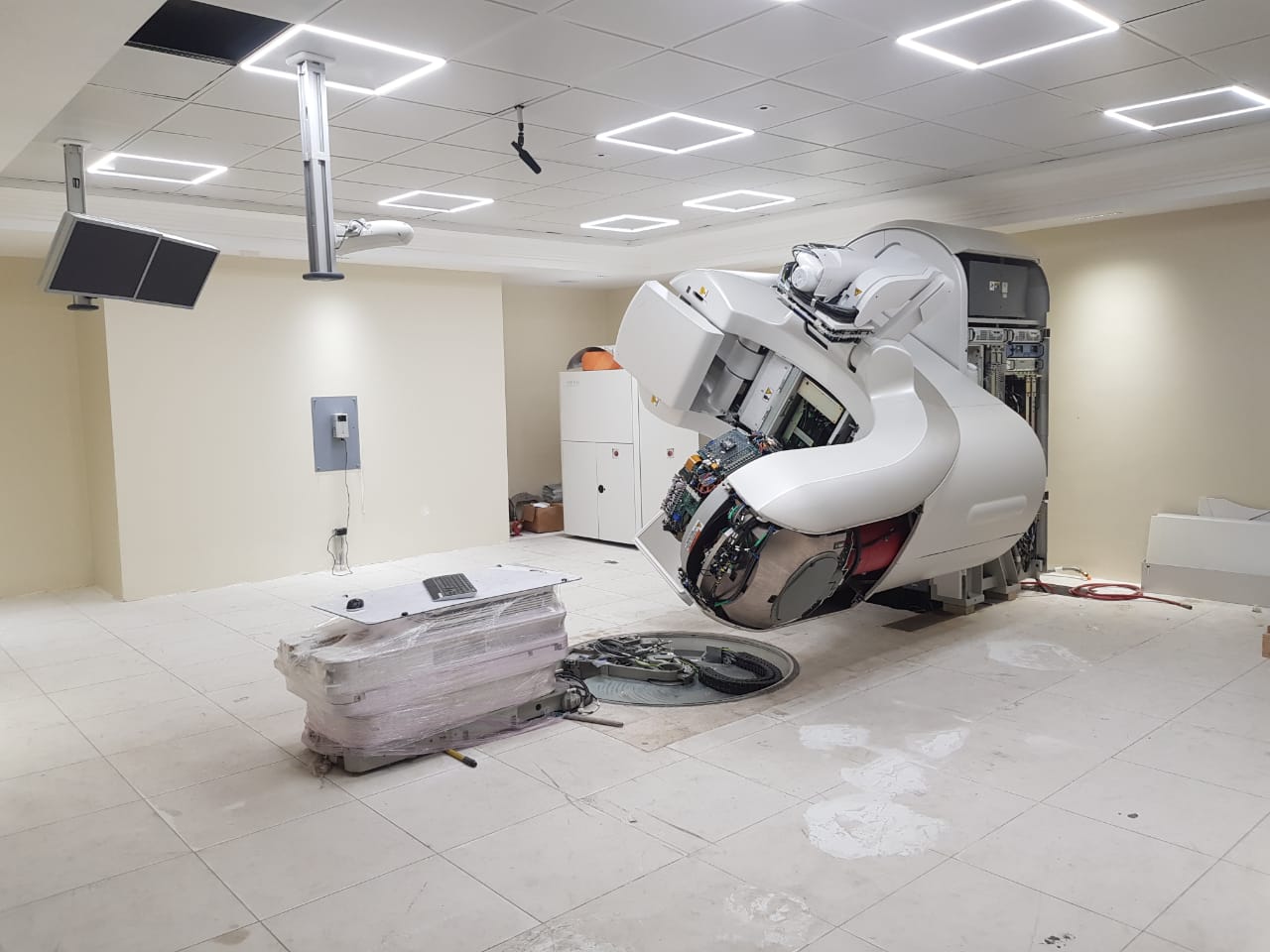
Linear Accelerator Installation Checklist: What to Do Before Your Linac Ships
Linear accelerator (linac) manufacturers and sellers typically require facilities to make certain preparations before their equipment ships. No one wants to be unready for installation when expensive equipment arrives. As the buyer of a linac, you are generally responsible for having to have most of the preparations in order, including those for the vault, radiation shielding, room build out, utilities, lighting, ventilation, air conditioning, mounting facilities, vault door, and access to the room ready by the day of installation. Otherwise, you will risk fees for extra time and travel, and other costs for storage, damage, and/or theft of the equipment while it sits idle at the site.
If this seems like a long list of responsibilities, keep in mind that the preparation process is your chance to make sure that everything goes smoothly on installation day and avoid regulatory issues now and in the future. About six months before your expected installation date (or longer, depending on regulatory requirements in your area), start working through the following steps. (Note: Each manufacturer has its own, specific requirements, depending on the make/model of equipment being installed. This is a general list to provide broad general guidance about what to of what is to be expected.)
In the Linac Treatment Room
Installation of accessories
1. If a base frame is needed, set it and grout it in place.
2. Make sure the relay junction box is installed, wired, and has wiring run to the modulator cabinet.
3. Emergency-off buttons should be installed and wiring pulled.
4. For incandescent lamps, install the warning light and make sure the wiring is pulled.
5. Install the laser light wiring, receptacles, and mounting plates, and verify their location, heights, and recess size.
6. Finish the walls (with at least a primer coat).
7. Complete the ceiling and verify its height.
8. Fully install cabinetwork, shelving, and storage in the treatment room (if doing so will not create obstacles in the rig path).
Check
9. Check the treatment room door and make sure related hardware is on hand. The door should be installed only if it doesn’t interfere with the machine rigging; otherwise, remove it for ease of access.
10. Verify that there is a clear opening for the linac. A path of 4’ x 7’ is generally okay.
11. Check that the room has the correct number of conduits, and that the conduits are clean, dry, and the right size.
12. If you ordered an in-room monitor, verify its location, mounting, power, and data cable conduit.
13. Review the minimum HVAC requirements for your new equipment, and make sure that your existing HVAC system meets the requirements and is operational.
Measure
14. Verify clearances for the rig path all the way from the unloading area to the vault. Again, use 4’ x 7’ as a general guide.
Test
15. Test that the main room lights and set-up lights are operational.
16. Make sure that water coolant is in the pit and valved below floor level, with a supply tested and available.
Schedule
17. Schedule a plumber and electrician to connect utilities to the machine no later than two days after the linac rigging is complete.
18. Schedule floor covering installation for after the linac has been rigged onto its base frame. We recommend doing this one week after the rigging is complete.
19. Contract riggers to move the equipment into the room, set it in place, and assist with assembling the major components.
In the Control Equipment Area
Check
1. Make sure all wiring is pulled to main breakers and into the vault.
2. Check that there is a main GE breaker panel, or an equivalent with 24VDC P/S.
3. Verify that there is an electronics cabinet opening for adequate cooling
Install
4. Finish the walls (with at least a primer coat).
5. Install floor covering, if it will not be in the linac rigging path.
6. Complete the ceiling and install lighting.
7. Set up a dedicated modem line (if remote diagnostics are being installed).
8. Complete cabinetwork shelving for the console
9. Set up an operational telephone at the console area.
When all of these preparation steps are complete, seal off both areas to ensure that construction dust particles from adjoining areas do not enter.
As a last step, review the paperwork: Make sure your architectural drawings have been reviewed by the Planning Department and a copy of the drawing review is on file. You will also want to keep a copy of your facility’s Accelerator/Radiation License on hand.
With this checklist and your vendor’s expert assistance, your preparation and installation should unfold quickly and smoothly!
Hi,
Do you have any recommendations/checklists for Bunker room preparations.
Thanks in Advance
Hiiii I am interested radiotherapy machine
Best blog so far I found, you have shared it in a detailed way, Keep sharing some more ideas on it. Always Air