In the highly specialized world of advanced medical equipment, some systems carve out a legendary,…
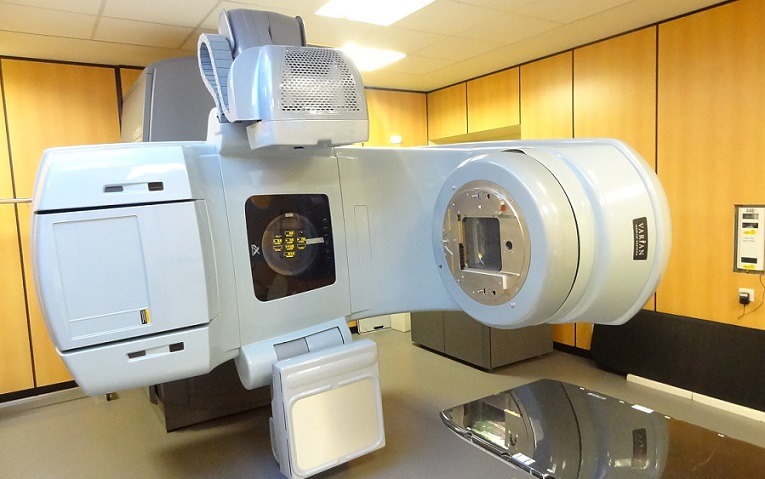
Considerations for Buying a Pre-Owned Linear Accelerator
When is purchasing a used linear accelerator a good idea?
Purchasing a used linear accelerator system is not recommended for every facility. New equipment is often a better solution for many customers. If your center requires the latest technology available in the market today, or if you are planning on installing a machine that will not be replaced for a longer period of time (at least in the next 10-15 years) then a brand new machine, or an almost-new machine, is often the better choice.
Many radiation oncology centers often struggle with the idea of new vs. used equipment.
However, it’s important to note that unless a linear accelerator was installed in the past week, it’s already a “used machine.” This means that virtually every linear accelerator system in operation today is already used.
Used linear accelerator systems may be suitable for facilities that fall into these circumstances:
- You are treating few patients (less than 8 or 10 per day, as a general rule) and may not have the revenue to sustain a more expensive machine.
- You live in a county or region where reimbursement rates are low and you are a clinic that must operate profitably to exist
- You will be using the linear accelerator in a limited manner, without the need for all of its technologies. For example, you are doing research and don’t plan on treating patients; you are treating pets or other animals and do not require a new machine; you are using only electrons to treat skin cancer for humans; or you are using it for non-medical, industrial purposes to image materials.
- You intend on buying new, more expensive equipment and technology in the next 4-7 years, but cannot afford it now and want to build up the revenue base of the practice.
- You are starting a new center and do not have a lot of capital or cannot secure financing to cover the costs of a new machine
- You have only one linear accelerator in your center, need to move locations, and can’t afford to have any down time.
- Software is more important to you than hardware (often, software is more expensive than the hardware anyway) in accomplishing your clinical goals and you don’t have the budget for both
- You need a backup plan to treat patients – especially if you are planning to upgrade your primary machine.
- You need a temporary solution while your new center is being built.
When given the option, most buyers would elect to buy a brand new, state of the art linear accelerator with the latest treatment technologies. With the realities of economics and current political policies, this is not always possible.
Purchasing used equipment does not lock your facility into operating dated technology. Newer machines often make it into the used equipment market, offering customers the ability to acquire the latest technology at a more affordable price. And many machines are also upgraded over time, as most original equipment manufacturers, as well as some third party manufacturers, offer upgrade platforms for used systems.
Used equipment is often a good strategy when building a new center. Many of ROS’s customers that initially purchased used equipment to build or start a radiation oncology practice, have later gone ahead to purchase brand new systems. In fact, the first-ever Varian Unique Linear Accelerator system sold in the Americas was sold to a customer that ROS helped launch with affordable, refurbished equipment.
Comments (0)